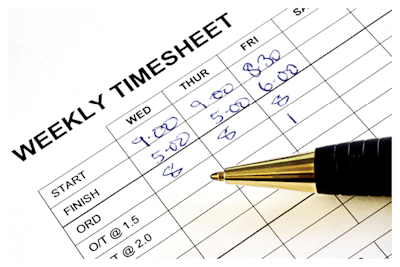
President Obama and Secretary of Labor Tom Perez announced May 18 a rule change regarding overtime regulations, which will impact not only more than 4 million workers, but also businesses of all sizes across the country — including cannabis businesses.
The Department of Labor’s (DOL) final rule raised the salary at which workers would be eligible for overtime from $455/week to $913 (from $23,660 to $47,476 per year). This means that any employees who make $47,476 or less per year (with some exceptions; more on this below) must be paid overtime (1.5 times the employee’s “regular” rate) for any hours worked beyond 40 hours per week.
The final rule becomes effective Dec. 1.
“This long-awaited update … will go a long way toward realizing President Obama’s commitment to ensuring every worker is compensated fairly for their hard work,” explains the U.S. DOL’s Wage and Hour Division on its website.
“The reason they put this into place is to protect people who are making, say, $35,000 a year and working 70 hours a week,” explains Kara Bradford, chief talent officer for cannabis staffing and recruiting agency Viridian Staffing.
Bradford says that the overtime threshold applies whether workers are salaried or hourly.
“This change affects all businesses and certainly will impact cannabis businesses,” says Mark Slaugh, executive director of the Cannabis Business Alliance. “The salary range now eligible for overtime extends to many entry-level and management positions in the industry.”
“[There] definitely will be an impact, especially for retailers that are not vertically integrated, so they are non-agriculture,” Bradford explains. “In certain states, for agricultural businesses, you don’t have to pay overtime. In other states, if anyone works more than 8 hours per day, you have to pay overtime,” she explains.
It’s important to check with your Human Resources executive or department, she suggests. For those businesses with no HR department, check your business classification and overtime laws with your state DOL or the organization that handles labor regulations in your state.
Because so many businesses in this industry are startups, and compliance with state/industry regulations consumes so much of a business’s attention, Bradford says, “I don’t think people are thinking about this that much.”
They should be, however, especially since many startups can’t afford to pay the highest wages, and grow teams are often required to work overtime, especially during harvest.
“Every business will need to look at whether they need to pay overtime, and in most cases, they will have to,” she says.
Slaugh says cannabis businesses will be harder hit by the new rule than other businesses. “The unique factor for the cannabis industry is the IRS 280E tax code, which unfairly collects tax from cannabis operations, without allowing for the same write-offs that other businesses receive, because of marijuana’s federal status. 280E effectively overtaxes the cannabis industry and pushes around 50 percent to 70 percent of industry profits into Federal coffers,” he says.
“Overall, the cannabis industry does not mind worker protections and complying with all laws allowing us to operate freely,” he adds. “However, the Federal Government needs to increasingly consider our industry when making policy changes that impact all businesses. Ideally, the Federal hypocrisy in expecting an industry they deem illegal to follow all business regulations without the same equality afforded to other businesses should come to an end as soon as possible.”
Who Is Exempt?
Under the DOL’s Fair Labor Standards Act (FLSA) guidelines, “white-collar” employees who meet certain requirements are “exempt” from overtime (and minimum wage), says Alex Wheatley, an attorney at labor and employment law firm Fisher & Phillips LLP. “Generally speaking, to be exempt … the employee must satisfy both a ‘duties test’ and a ‘salary test.’ Under the duties test, the employee must perform executive, administrative or professional duties,” explains Wheatley, “and each of those categories have their own requirements.”
The duties test did not change with the new overtime rule, he says. However, the salary test did.
“Many employers will find that employees they previously paid between $23,660 and $47,476 per year do meet the duties test, and they now have to either increase that employee’s salary to pass the salary test or convert that employee to a non-exempt employee and pay overtime,” Wheatley says.
He stresses that while the duties test did not change, the new overtime rule should “serve as a reminder to all employers to make sure that the employees they are treating as exempt do pass the duties test. Even if you pay someone $90,000, if they do not meet the duties test, the employer must pay overtime,” Wheatley says.
There is another exemption, he notes, for “highly compensated employees” who make more than $134,000 per year (which is an increase also imposed by these new regulations, up from $100,000).
What Should Cannabis Business Owners Do?
“All employers will now have to consider adjusting base pay for employees in comparison to the hours those employees work and whether the marginal cost of overtime is more or less than the marginal cost of increasing or decreasing base salaries for these employees,” Slaugh says.
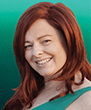
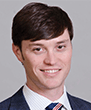
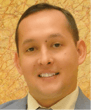
Tom Regan, president of cannabis cultivator and retailer Mindful Colorado, is in the middle of that process.
“We are currently about halfway through converting our qualifying employees,” Regan says, “and we have found that the key is to take this mandatory action with sensitivity and understanding for our employees and their individual roles.”
“It is important to remember that employers can forbid employees from working overtime without authorization and can even fire employees if they work overtime without authorization,” Slaugh adds. “Though, if the employee works any such overtime hours, the employer must pay the overtime premium even though the employer is firing the employee.”