Workers at R. Greenleaf Organics in Albuquerque, N.M., have to be committed to maintaining a clean, contaminant-free growing environment. Jacob White, chief of cultivation, makes sure nobody cuts corners when it comes to cleanliness.
“I have always believed the two most important things in medical cannabis production is No. 1, cleanliness, and No. 2, your environment,” White says. “You can have the best strains in the world, but if you don’t have a good environment you’re limited in what you can do.”
That’s why White knew he needed to make a change in late 2015. The presence of powdery mildew in 13 of R. Greenleaf Organics’ 14 cannabis grow rooms indicated something was wrong with the environment. Powdery mildew is a fungal disease that thrives in high-humidity conditions. The disease reduced overall yields by at least 25 percent. In one room, 70 percent of the plants were lost, says White.
White attributes at least some of the losses to a lack of automated controls. R. Greenleaf Organics had moved to a 14,000-square-foot warehouse in January 2015. Due to budget constraints, the company relied on rudimentary controls, such as non-programmable thermostats. This January, White installed controllers for each room that automatically adjust CO2 levels, humidity, temperature and lighting based on set parameters.
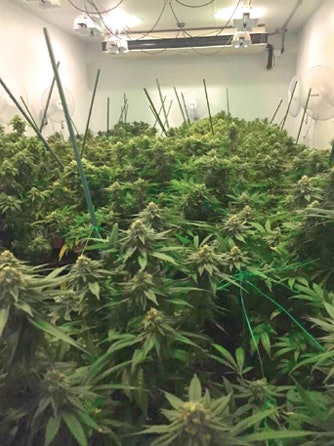
Most importantly, R. Greenleaf Organics has not experienced a recurrence of powdery mildew since implementing the automation system, White says.
Automation may include controllers that regulate environmental conditions, such as humidity, temperature, CO2 levels and light or mechanical systems, such as irrigation systems, seeders or potters.
More than two-thirds (68 percent) of cultivators say they’re using technology to automate temperature control, according to Cannabis Business Times’ 2016 “State of the Industry Report.” More than half of the growers who participated in the research say they use humidity-control technology.
A Maturing Market
The trend will continue to grow as the industry matures, says Michael Mayes, CEO of Quantum 9 Inc., an international cannabis consulting firm based in Chicago. As the industry moves from craft producers to larger-scale enterprises, growers, especially those in newer markets, are incorporating automation into their plans, Mayes says.
Growers in older, more-established markets, such as California, may not have facility designs that were optimized for sophisticated automation systems because of tight cultivation limits, Mayes says. But growers constructing new facilities are beginning to incorporate automation into their building designs.
“Or, they are retrofitting a building that was used for heavy manufacturing, and before any plants go into the facility, they have the ability to build it to spec and run automatic fertigation lines throughout the entire facility,” Mayes says.
In some respects, cannabis facilities are more advanced than traditional horticulture operations because of the younger workforce involved and the unique environment that’s required for cannabis, says Patricia Dean, CEO of Wadsworth Control Systems. “We’ve been in business for 50 years, and these cannabis operations have more equipment than a lot of facilities,” Dean says. “They’re a bit more automated, high-tech than a lot of other horticulture markets.”
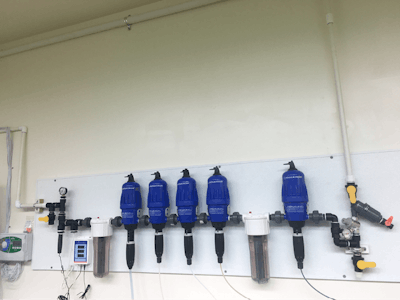
Perhaps because many are younger, cannabis growers tend be more familiar with technology, Dean says. Also, because they’re producing high-value crops, they often work under tighter parameters and are more concerned about optimal humidity levels and CO2 than traditional markets, such as floriculture, she adds.
Some material-handling systems can involve larger capital investments, but present great opportunities to the cannabis industry, says Bill Bissell, senior process design specialist for AgriNomix LLC, an Oberlin, Ohio-based supplier of automated production equipment for growers, from soil mixing, cloning lines and potting machines to fully automated bench movement systems. “We often see smaller grows benefit the most from a piece of automation. They are the most labor-limited folks, so bringing [in] an automation tool ... can be a life-changer,” Bissell says. Such automation is commonplace in other horticultural facilities and can easily be applied to cannabis, he adds.
As the industry matures, price competition heats up and efficiencies must be taken even further to lower production costs, including labor and related processes, industry analysts and another vendor CBT spoke with say these technologies will become more commonplace in cannabis as well.
In fact, according to Zev Ilovitz, president of Envirotech Greenhouse Solutions, many growers are already making the shift to automating production processes to reduce labor costs. “There is strong interest in mobile bench systems. The efficiency of the cultivation system is greatly increased by moving plants to people rather than people to plants. While mobile bench systems have higher infrastructure costs, customers are realizing that the difference compared to a stationary or rolling bench system is paid back rapidly with the labor savings that the mobile system provides,” he says.
“Mobile bench systems are very flexible; they can be operated manually, or motorized, in a single or multi-level system,” he adds. “The design and function of a system will often depend on the scale, style and sophistication level of the cultivation facility.”
Less Work, Greater Yields
Perhaps one of the reasons some cannabis cultivators hesitate to completely automate is their belief that technology should complement human interaction with plants rather than replace it. That’s the approach Denver-based Good Meds — which has a 90,000-square-foot cultivation facility and two dispensaries — typically takes with its cultivation operations, says Good Meds founder John Knapp. But in at least one area, automation won out over a hands-on approach.
Good Meds opened its current cultivation facility about three years ago. Initially, the company relied on hand-watering and manual fertilization. The process left too much room for error, says Knapp. Employees would get formulations wrong or forget what nutrients they already mixed into the fertilizer tanks.

In early 2015, Knapp implemented Dosatron fertigation systems for each room. Fertigation involves the injection of nutrients directly into an irrigation system. Total system and installation costs were $80,000, and total installation time was about three months, according to Knapp. The cost includes a complete replacement of the facility’s irrigation system to accommodate the Dosatron units.
A series of Dosatron pumps, connected to irrigation pipes, suction nutrients from a tube placed inside fertilizer jugs. The pumps then inject the fertilizer into the water lines based on a dial setting. The mixture flows to drippers located at each plant. The system ensures the precise amount of nutrients are being dispersed at a set gallon-per-minute rate, Knapp says.
Good Meds has realized a 20-percent to 40-percent increase in yields and recouped its investment in the Dosatron systems in less than one harvest, he notes, adding that “even a couple percentage points increase in yields would have paid for that within six months.”
The system also reduces the amount of time employees must spend watering so they can focus on other important tasks. “At the end of the day, watering plants is important, but you also have to prune them, you have to train them, you have to make sure the environment is right, so it gives the guys way more time to work on optimizing everything else,” Knapp says.
Preventive Maintenance
Likewise, for R. Greenleaf Organics, the investment in automation paid for itself quickly and has helped employees focus on other critical activities. “We can put all our energies into growing cannabis and less time worrying about environmental conditions,” White says.
The company, one of three nonprofit businesses operating under R. Greenleaf & Associates, has implemented fully integrated environmental controls in three flowering rooms, and upgraded the thermostats and controllers in the remaining 11 rooms to digital, programmable units.
The automated systems also have data-logging capabilities, which helps White identify issues before they become a major problem. Recently, one of the rooms experienced temperatures that were well above the set limit. By observing data patterns, White could see the issue was happening during the evening and that it was a problem related to the air conditioner. Without the data log, White says he would have likely checked the controller first.
White and the company’s director of operations installed the system at a cost of about $250 per room. But White says he wants to eventually have a single environmental controller for all of the flowering rooms.
“To get a system installed to meet all of our needs, the cost has been quoted as anywhere from $1,500 to $3,500 per room,” White says. “While this is an expense to be planned for, it will easily be evened out by prevention of further infestations.”
Looking Ahead
Implementing an automation system brought some challenges for White. “A lesson learned was to trust, but verify what hired contractors are selling you. We thought we had purchased one thing, and were given another, simply by completely trusting the contractors at face value,” he says.
As he tries to move toward a single control system, he has received contractor proposals that vary widely. “My expertise is in growing, and not HVAC,” White says.
For many cannabis growers, their ability to scale up will depend on their knowledge of business systems and practices that might, at the outset, be unfamiliar.
White says he has had to ask more questions of suppliers, regarding the different aspects of each system, to be able to gain a better understanding of the systems he is considering and the differences between each.
Cultivators also shouldn’t hesitate to consult with the agriculture industry for advice on technology, Knapp says.
“This industry has come out of the black market. So the knowledge and the people that do this kind of stuff don’t necessarily have the typical agriculture background,” he says. “It’s interesting to watch how the industry came up, and the type of techniques and tools employed in the beginning and how it’s evolving. There’s a lot more influence from the agriculture industry [taking] hold.”