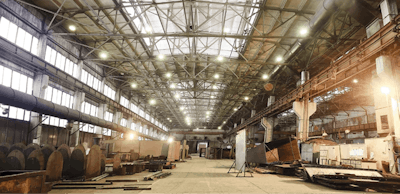
With commercial cannabis cultivation being permitted in more states, counties and cities, cultivation and extraction facilities face increased scrutiny from state and local regulators for potential violations. Therefore, a building’s design is a critical consideration when selecting a location for your cultivation and extraction operation. Mechanical, electrical, plumbing (MEP) and structural engineering will play a huge role in your facility’s success.
As such, not conducting proper due diligence can be costly. I’ve seen clients miss deadlines because the facility they selected needed more work than anticipated, or wasn’t zoned correctly, which caused them to lose their licenses. Putting together an experienced team before facility selection will help you avoid such issues. You want your architect and MEP engineer(s) to have experience with at least a few cannabis cultivation and extraction facilities, as the building requirements are much more stringent than typical commercial buildings.
In addition to building a solid team, here are eight things to look for when shopping for a facility.
1. Zoning
First and foremost, find a building properly zoned for cannabis cultivation. There are instances where a cultivator signed a lease for cannabis cultivation prior to going through the licensing process to find out that the building wasn’t in an area zoned for cannabis cultivation. Most cities or counties have zoning maps available depicting “Green Zones” (areas or properties that qualify for cannabis operations). You don’t want to invest in a new venture only to discover you can’t operate because you didn’t do your homework.
2. Parking
Recently, my firm provided the MEP design for a Long Beach, Calif., extraction facility. The client’s architect provided my firm with floor plans. The plans were submitted to the city by the client, but were denied due to insufficient parking. The building was constructed decades earlier when parking regulations were much different than they are now. Due to this, additional parking had to be added. Prior to leasing or buying a building, check with your local building/planning department to find out if you’re required to add additional parking, including handicap-accessible, for an existing building. (See the example to the right for parking requirements in the city of Long Beach for medical marijuana facilities.)
For starters, this caused a major issue because the client wanted to expand the building slightly. Overall, the addition of more parking space affected the architectural plans, which also affected the MEP drawings. We were forced to redesign the facility, costing the client more time and money.
3. Building Insulation
If you’re purchasing or leasing a warehouse, it’s imperative that you understand your insulation requirements to maintain your grow temperature. In California, we must adhere to Title 24, which governs energy efficiency. Unless you build insulated cannabis grow rooms within the warehouse, you will have to insulate the entire warehouse, which adds additional expense.
4. Electrical
Ensure the location has the electrical capabilities you need. Hire an electrical engineer and discuss the loads you want to use so he or she can determine total amps needed.
Voltage is also part of the equation. Ideally, you want 480V (volts), 3 phase, as this gives you more HVAC and grow light options. With grow lights, the higher the voltage, the more lights you can put on a single circuit. (See the box to the left illustrating this.) Reducing the number of home runs (main circuit connected to multiple lights going back to the panel) will reduce the amount of wire, metal conduit and labor, which will save you money on large grow operations.
If you can’t find 480V systems—208V, 3 phase, would be the next best. Avoid 240V, 3 phase delta systems. Delta systems are usually found in old buildings and essentially have three different voltages (120V, 208V and 240V). As shown in the diagram to the left, 240V, 3 phase delta systems have a “wild leg” (sometimes called a “stinger leg”). On a typical 208V, 3 phase wye system, if you placed a voltage probe on any leg and placed the other probe on neutral, the volt meter would display 120V. On a 240V, 3 phase delta system, if you measured between the “wild leg” and neutral, the volt meter would display 208V.
These systems can be a nightmare to design around and can be costly due to the additional electrical panels you may need. For example, if you have several electrical components that use 120V (i.e., circulating fans, general receptacles), you would have to avoid the “wild leg,” leaving a large percentage of your circuit breaker slots empty (unless you have other 208V loads). With so many unused slots, you may have to install additional subpanels. Delta systems can work, but they add another layer of complexity.
If you buy a building with 240V single phase, plan your grow room in advance. We recently had a client with a 240V single phase, 200A service, and we had to cycle rooms at different times. We had another client who had 240V single phase, 400A service, but had to purchase expensive phase converters to turn single phase into 3 phase to power heavy-duty extraction machines. Again, these scenarios cost the client more time and money.
Make sure you also consider the local power grid. You can have a perfect building, but if the local grid can’t support your power requirement, you will be up the creek without paddles. If you’re building from scratch, engage the local utility to determine whether enough power is available to meet your needs.

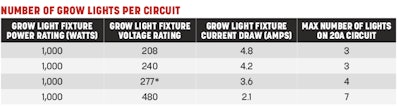
5. HVAC
When leasing a building, ensure your landlord understands the potential facility modifications for indoor cultivation. For example, indoor cultivation requires significant HVAC, so make sure your landlord knows about the impacts to the building’s roof.
We recently provided the MEP design for a large, indoor cannabis facility where the client specified that the condensing units were to be placed on the roof. After the design had been completed, we discovered that the client didn’t consult the landlord, who was not happy. We had to redesign the MEP drawings.
In another instance, the client insisted on rooftop units, but the landlord had not provided a reinforced roof as previously agreed upon. Therefore, the roof could not withstand the additional weight.
If you plan to put the condensing units on the ground, make sure you have enough space for them (typically 3 feet working clearance). Quite often there is not sufficient space due to clearance requirements or required parking.
6. Sewage Capability
Also when leasing, make sure you understand sewage requirements. If you have a public sewage system, ensure that the main sewage line is large enough for your planned operation by determining your facility drainage requirements, which include restrooms, HVAC condensation and grow room sinks and floor drains.
If you have a septic tank system, confirm the tank size and leach field is adequate for your needs, just like you would for a public sewage system explained above. A septic tank essentially holds all the solids while the excess fluid flows to a leach field and drains into the soil. If the septic tank is not sized adequately, you must account for the additional cost to replace it. If the leach field is not adequate, a percolation test (a test to determine soil’s water absorption rate) will need to be conducted. Typically, your city or county should have the results of the initial test; however, there have been instances where the records were lost or thrown out due to the age of the building you plan to buy or lease. Also make sure the septic tank has been inspected.
7. Demolition
When selecting an existing building, consider demolition costs. If you discover a building that was previously used for product manufacturing, you’ll find that demolition could potentially be very costly. Sometimes old equipment and abandoned electrical panels can be left behind, leaving you with a mess to clean up.
Large, heavy equipment can be expensive to remove, especially components that are hung from the ceiling such as forced air units (FAUs). Removing large condensing units off the roof can also be costly. Depending on the condition of the equipment, scrap metal companies may remove the equipment for free.
8. Past Tenants
Another consideration is how the previous tenant used the facility. One of my first projects was re-purposing a large warehouse. After the client signed the lease, completed the architectural plans and contracted my firm to do the MEP design, we discovered that the previous tenant used the facility for microchip manufacturing—a process in which toxic chemicals are used. The health department was concerned that chemicals may have leaked into the soil. Luckily test results came back negative—but if they had been positive, the client would’ve had to pay significant additional fees to make the building safe again.