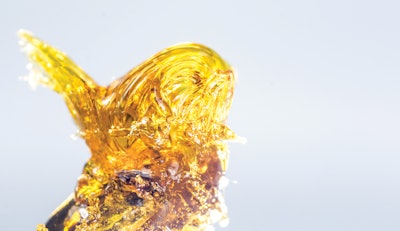
The cannabis concentrate industry has advanced at an accelerated rate for the past five years. In fact, more advances to specialized, large-scale equipment and the associated methodologies have occurred in the past five years than all previous years combined, thanks in large part to the influx of funding for research and development.
This unprecedented acceleration has produced a completely different focus on concentrate manufacturing. Like all other agricultural commodities, today’s focus has shifted from simple production to lowering cost of production without compromising quality—i.e., catering to customers’ desires for the best possible product at the most affordable price.
As of late, I’ve been seeing market movement toward wet-plant extraction. This method does not require trimming, drying or curing plant material, which saves money on trimming-labor costs and construction and maintenance of drying environments. And since the terpenes are not evaporated during drying, it yields a final product with the highest monoterpene content. Combine this methodology with large-scale extraction equipment and processes, and you can produce superior products for a superior price. That said, the resulting multitude of concentrate forms have specific and targeted uses, ranging from flavorless distillates for manufacturing edibles to full-flavor, high- cannabinoid content oil for vape cartridges, and everything in between.
The first installment of this extracts series sheds light on different extraction methods and their resulting extracts, and explores the cannabinoid and terpene profiles of each concentrate product and its intended end use.
What’s In?
Today, multiple large-scale extraction methods are available, and more are being developed to facilitate large-scale CBD extraction from hundreds of acres of hemp fields being cultivated in many U.S. states, Canada and Europe, among others. Medium-scale methodologies are being utilized to manufacture most connoisseur-quality and mass-produced consumables in various concentrated forms, but large-scale processing and manufacturing soon will match that quality.
Less than 10 years ago, cultivators had few extraction-equipment options, let alone large-scale extractors or super-refining equipment. Manufacturers were reluctant to sell equipment to or advise anyone in the cannabis industry during prohibition. Realistically, cultivators had five options:
- carbon dioxide, or CO2, extraction (done crudely);
- dry sieve;
- water extraction;
- basic Soxhlet extraction methods; or
- crude cold finger extraction methods.
Today, some of those methods have been scaled and perfected and can produce quality products, and many other equipment manufacturers have emerged. Competition between those manufacturers has accelerated development and innovation, resulting in more diverse apparatuses often borrowed from existing industries that have produced extracts and equipment for decades (e.g., U.S. Patent No. 4,276,315, filed in 1979 to patent a method of decaffeinating coffee). Other equipment manufacturers have expanded the capabilities of their larger equipment and focused on efficiency through automation.
Here is a breakdown of current methods employed and of extraction equipment in rapid development.
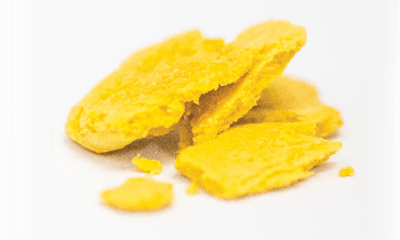
CO2 Extraction
CO2 extraction has been employed for decades, yet CO2 cannabis extraction is relatively new because of prohibition. Therefore, as already mentioned, manufacturers have only recently started perfecting equipment and practices to produce high-quality extracts rather than crude extracts that were labor-intensive to super refine into sellable products. Still, CO2 extracts often require further refinement, depending on the end use or desired product purity and potency.
CO2 extraction requires that cannabis material be dry—and the dryer the better. Because of that, the majority of available monoterpenes (myrcene, alpha-Pinene, beta-Pinene, limonene, linalool, terpinolene, just to name a few) are evaporated during the drying process, resulting in a product with a much lower terpene content than the plant material from which it came. That’s not to say all terpenes are eliminated, but most of the terpenes responsible for the full expression of the plant are. This makes it a perfect concentrate for manufacturing edibles, especially those that don’t taste or smell like cannabis, which many consumers and patients prefer.
CO2 extraction is a great method of extracting cannabinoids that can then be super refined via winterization, filtration and distillation. Many extractors employ CO2 as a primary extraction method, then further refine the extract into desired compounds for a variety of uses and products, ranging from edibles to topicals and oil cartridges (often infused with either non-cannabis or cannabis-derived terpenes that are added to the extract). Yields depend on both the percentages of available cannabinoids/terpenes in the plant material being processed and the skill of the technician/operator.
Hydrocarbon Extraction
Hydrocarbons, whether butane or propane (or others), have also been employed as a form of extraction in other industries for decades. However, utilizing hydrocarbons to extract cannabis at a large scale is, again, relatively new.
A decade ago, cannabis processors extracting with butane used cans of lighter fluid in a process termed “open blast,” and closed-loop extraction systems (which do not evaporate the solvent into the environment) were merely a dream. The unprecedented rise in demand for, and sales of, hydrocarbon extracts has dictated a rapid acceleration of development of available closed-loop extraction systems, which has massively improved safety and efficiency. Production costs are lower, thanks in part to new equipment that enables the butane or propane to be recycled instead of boiled off.
Hydrocarbon extraction can be performed using dry or wet plant material. (Wet material is used if processors want to focus on monoterpene preservation and extraction.) The process is rather basic: Super-refrigerated solvent is passed over plant material in a sealed vessel, stripping the cannabinoids and terpenes from the plant material and binding them to the solvent. The solvent is then removed from the cannabinoid/terpene-rich liquid and returned to the original containment vessel from which it came. (Each manufacturer and equipment manufacturer utilizes different temperatures depending on the desired reaction, be it refrigerated solvent, double-jacketed columns cooled with liquid nitrogen, or de-waxing columns and filters also cooled utilizing liquid nitrogen.)
The resulting concentrate is left behind in a collection vessel, while the concentrate can be further refined or made into many different forms of products, including:
- Oleoresin: a natural or artificial mixture of essential oils and a resin in the form of a semi-solid extract;
- Absolute oils: concentrated, highly aromatic oily mixtures extracted from plants, produced through solvent extraction;
- Concrete: in perfumery, a semi-solid, solvent-extracted mass made from fresh plant material.
These are proper terms for various extract forms, but as the cannabis-extraction industry progressed, it invented its own terminology to describe the varying final forms of its extracts. Most of these cannabis-specific terms are based on observations such as color composition, form or action. For example:
- Budder: As the name implies, this concentrate form is light in color and when heated, has a consistency similar to warm butter. It can be manufactured utilizing hydrocarbons, ethanol, alcohol and rosin as well as alternative methods. If made properly, it has a very high cannabinoid and terpene content.
- Shatter: Typically a solid/hard concentrate that can range in appearance from translucent to opaque, and from red to golden-amber. It is most commonly produced in a vacuum-drying oven after extraction. It is high in THC, but as with most harder-consistency extracts, it has a lower terpene content than budder or wax.
- Wax: This form has a warmed-wax consistency. Its color can range from off-white to golden-amber. Most often it is manufactured by agitating hydrocarbon extracts after extraction, but can be made by a multitude of extracts.
- HTFSE/HCFSE (high terpene full-spectrum extract/high cannabinoid full-spectrum extract): A hydrocarbon extract or alternative extract that has been extracted with a specific focus on a high percentage of available cannabinoids. The cannabinoids and terpenes separate naturally, allowing for custom blends.
Besides these forms, the industry has been further refining cannabinoids into their purest forms, from crystallized extracts of CBD to THCA, Delta 8, THCV, etc., at 90-percent purity and higher.
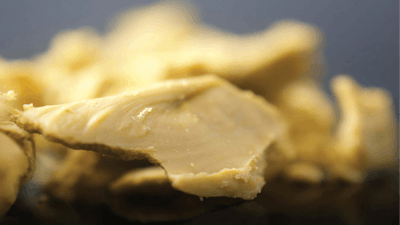
Other Extracted Products
While the aforementioned staple concentrate forms have been popularized over the past five years, other extraction methods have been around for hundreds—even thousands—of years.
For example, hand-rubbing, or dry-sieving, is a method that utilizes specific-sized screens to make hash. In this method, the cannabis is agitated over the screens, and the resin glands are separated by size.
Water-extracted hash is produced in similar fashion to the sieve method, except the cannabis is submerged in water and gravity allows the resin glands to sink and separate. Dry-sieve hash has a higher terpene content than water-extracted hash because a portion of water-soluble terpenes are lost in the water.
Rosin is a form of concentrate that is relatively new. Its manufacturing process involves the application of heat and pressure to dried cannabis buds. When pressed and heated, the available resins containing cannabinoids and terpenes are squished out and collected en masse.
Recently, liquid nitrogen (LN2) has been becoming a common initial form of extraction. In this method, wet or dried cannabis is submerged and agitated in large conical tanks. The resin glands are separated and collected in a manner similar to water-hash separation. This method yields a terpene-rich extract in a form that can be further processed into any other form (such as pressed hash, rosin, CO2 extracted for refinement, hydrocarbon extracted for refinement, or further refinement via distillation into an oil), depending on the desired final concentrate.
Ethanol alcohol extraction on a large scale is another industrial application that is just now becoming available to the cannabis industry. In this process, the cannabis is soaked and agitated while submerged in ethanol, and the alcohol absorbs the cannabinoids and terpenes (along with some undesirable compounds requiring further refinement to eliminate). The cannabinoid- and terpene-rich ethanol alcohol is winterized and filtered, then refined via rotary distillation or other form of distillation to remove the ethanol from the extract and recover it for re-use. After refinement, the resulting concentrate is an oil with high-THC content that ranges in color from clear to amber. This oil can then be utilized for a variety products and formulations similar to CO2 extract products.
Distillation (either thin film, wiped film or short path) is also a popular methodology that was scarce even five or so years ago. The process typically involves heating the concentrate to remove any non-cannabinoid impurity. Typically, it is utilized for super refinement of cannabinoids, whether THC or CBD. CBDA or THCA cannot be produced through distillation (unlike with hydrocarbon extraction) as the acid forms of those cannabinoids convert to their regular forms in the presence of high heat. For the most part, distillation is utilized to remove and recover alcohol from extracts and to target boiling points of specific cannabinoids. Distillates can be utilized to formulate or manufacture most any desired product or incorporated into vape cartridges.
All the above-mentioned products share one thing in common: Yields are typically dictated by the quality of the starting material, operator skill and whether the output goal is quantity or quality. Ultimately, the extraction method you choose should be based on your desired final concentrate form.
So which form should you be producing? Part II of this extracts series (which will be featured in the September issue of Cannabis Business Times) will help you understand the considerations that should go into making that decision. Stay tuned.